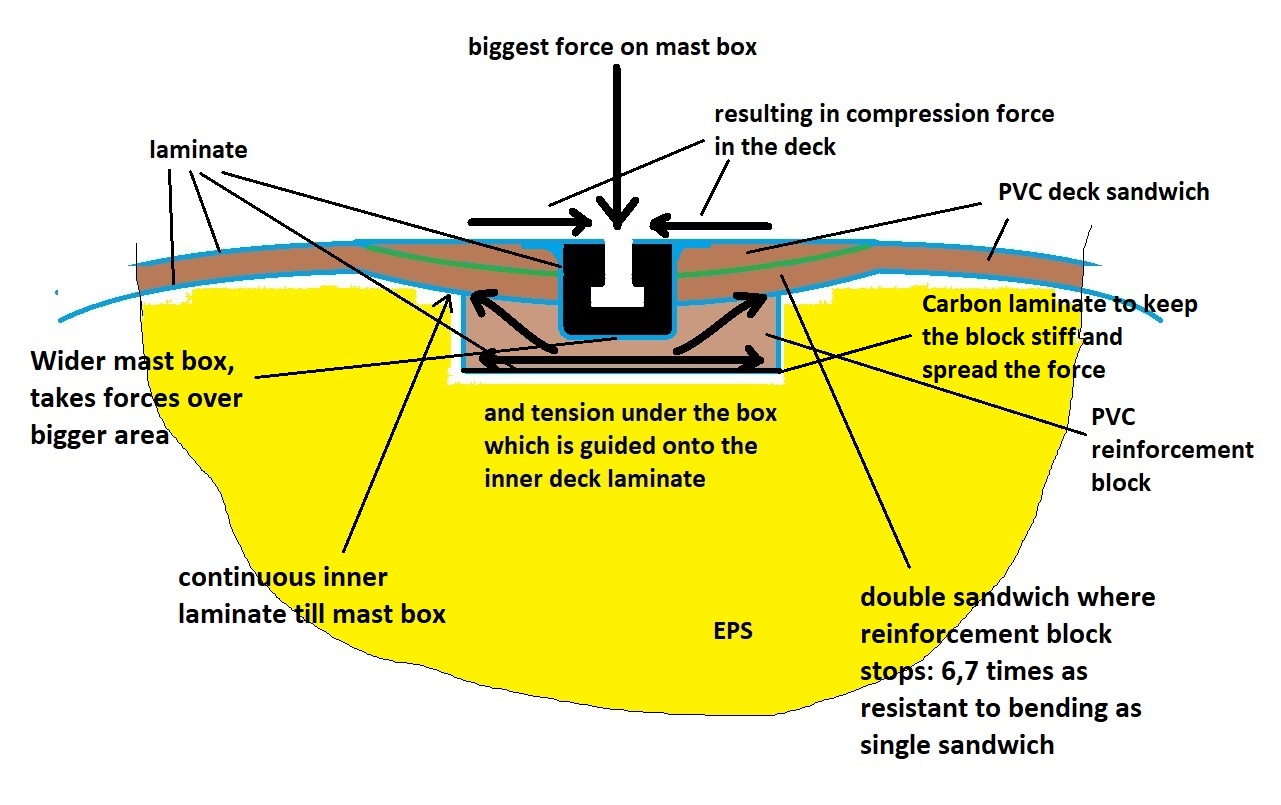
Those Small but Significant Differences Part 4: Mast boxes
April 26th, 2020 Posted by Bouke Becker Boards No Comment yetMast box constructions
Today we are looking at different mast box constructions. Our standard mast box construction, the standard mast box construction of regular production boards and the construction of pre moulded carbon boxes into a PVC block.
Forces
The biggest force on a mast box is vertically from flat landings. Another force can be a pull force on the nut when tightening the mast foot and especially getting washed by waves. As a mast foot is made to bend, there are hardly any leverage forces like on a fin box.
For the vertical down force, it is important that the force is spread out over a big area of the EPS. This is achieved by making the area resistant to bending. And the best way to do this is by having a thicker PVC. The pretty much standard PVC reinforcement block around the mast box already spreads the force out over a bigger area. The wider and longer the block, the better the spread.
Though we have seen some custom brands where the boxes were just put into the EPS and nothing else, sometimes with glass, sometimes even just with resin. Steer clear of such boards.
Both Witchcraft and regular production boards place the PVC block before the sandwich. Like this the inner laminate under the sandwich continues till the box itself, with an overlap of laminate with the PVC block. Boards that use a pre moulded carbon mast box need a much bigger hole cut into the deck sandwich to mount the block after sandwiching. Here the inner laminate is cut through and just makes a blunt connection without an overlap, creating a weak point at this spot. For a sandwich construction both inner and outer laminate are equally important. This weak point is more prone to break when the PVC block is not extended long enough at either end of the mast box and the mast foot is mounted more towards either end and the mast foot does not sit fully on the PVC block any more. Normally an adjustment of a few cm already is enough so we like to keep the box short.
Then, apart from the PVC block, we also put a bigger area of double sandwich around the area of the mast box.
As the resistance against bending goes up exponentially with the sandwich thickness, a double thick sandwich is about 6.7 times as resistant. We also taper the double sandwich away so the inner laminate can be continued and does not need a second layer.
Here the view from our CAD/CAM program showing the reinforcment block and the double sandwich area and in the second all the blocks and inserts, which are all milled by CNC to the 0.1mm exact and saves a lot of measuring time. The asymmetric positioning of the mast box is on purpose as the back part of a mast box can´t be used. There are parts we do not show and also the mast box construction of the HDD and XHDD is very different than this but we don´t want to reveal too much to our competition.
Here is the cross section of a pre moulded carbon mast box:
Here is how the inside of a regular mast box construction looks like:
Injection moulded plastic boxes with a high content of glass fibre are slightly heavier than carbon boxes. We use a pretty short “(ST)RONG” box from Chinook which weighs 65 to 80gr.
The Chinook boxes we use have a high content of glass fibre inside the plastic which is injection moulded under high pressure. These boxes are very though and consistent in quality. There is also more material holding the nut. Chinook boxes have another useful little detail and that is a small notch at the back so that if the mast foot becomes unscrewed a little, it still can´t slide out which can cause some dangerous situations and loss of your board or entire equipment.